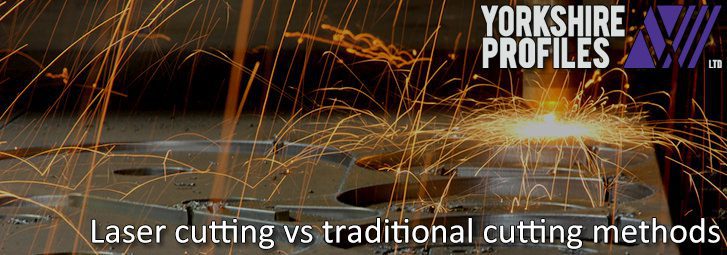
At Yorkshire Profiles our favoured method of sheet metal profiling is laser cutting. With an Amada F1 Co2 laser installed and the intention to install a faster, more efficient and environmentally friendly fibre laser in the near future, we are a fast growing laser cutting company.
But, laser cutting isn’t all there is in sheet metal profiling! A variety of other methods can be used. In fact, we began our company not as a laser profiler, but with a waterjet cutter!
In many areas of industry, including ours, laser cutting is favoured because of its comparative speed, accuracy and affordability when considering all of the cutting methods available. But there are alternatives within laser cutting itself.
Laser Cutting
Laser cutting uses a highly concentrated stream of photons to cut precise designs in sheet metal. Laser cutters like ours are programmed using Computer Aided Design (CAD) software providing high levels of accuracy to every cut as we programme each variable (metal thickness, type and subtype, speed of cut and laser intensity ratios) into our software for the laser to action in cutting the sheet metal. With the automation of the laser cutting itself and the installation of an automatic feeder shuttle table for the metal, we can run sheet metal through the process without having to constantly monitor the machine, allowing large volume work to be completed over night with the machine left unattended.
Our laser cutting machine cannot be used to cut plastics (they melt), wood (it burns) or metals that are considered to be “shiny” when molten – meaning that they have a low melting point and melt under the photon beam of the laser, like brass and copper. This is not to be mistaken for “polished” as we can cut mirror polished stainless steels. For these materials the alternative cutting methods are more suitable – such as waterjet cutting or mechanical cutting (using a band saw, for example). Our laser cutter also cannot be used to cut tubes, we have a band saw for that!
There are 3 main types of laser cutting, each with their own advantages and disadvantages. Generally speaking the advantages of laser cutting as listed above are accuracy, speed and affordability, and the disadvantages are the limitations on material thicknesses and types. Let’s take a closer look at how laser cutting compares with other cutting methods, starting with our previous method, Waterjet cutting:
Waterjet Cutting
At the beginnings of our company we had only one machine – a Waterjet cutter. This machine served us well but proved costly to run, slow, and lacked accuracy on smaller parts. So we installed the laser cutting machine, running both for a few years before ultimately removing the waterjet.
Having both the laser and waterjet provided the benefits of both machines, but as precision engineering became more popular the need for the waterjet’s ability to cut through thick metal sheets, woods and plastics dried up and the machine was replaced here with a second press brake and other fabrication tools so that we can offer a more rounded service to our customers.
In waterjet cutting a jet of pressurised water as high as 60,000lbs per square inch is fired into the material nested on the bed to cut through almost anything. This water can be mixed with abrasive grain to cut through thicker materials and close tolerances.
The main differences between our CO2 laser cutting and our previous waterjet cutting are shown in this table:
Our Amada F1 CO2 Laser | Our previous Waterjet Cutter | |
Energy used | Light | Water |
Source of energy | Gas powered laser beam | High pressure water pump |
Transmission of energy | Laser beam guided by mirrors | High pressure hoses |
Maximum permissible tolerance & distance between material and nozzle | +/- 0.1mm | +/- 1mm |
Physical Machine Set Up | Laser source located inside the machine | Waterjet cutting area exposed, pump located separately |
Beam output | 1500 to 4000W | 4 to 17 kW (4000 bar) |
3D Material Cutting (tubes) | Not possible due to rigid beam and strict CAD regulation of distance to nozzle | Partially possible. Residual energy behind material dispersed by water |
Materials able to be cut | Metals, excluding reflective metals such as brass | All materials |
Material thicknesses able to cut | Up to 25mm Mild Steels, 12mm Stainless Steels, 10mm Aluminium | Up to 1 foot thick in most materials |
Common applications | Cutting flat sheet metals | Cutting stone, plastics, ceramics, thick metals, reflective metals |
Parts that will wear out with use | Protective glass, gas nozzle, mirrors | Nozzle, focusing nozzle, pressure components, hoses, seals, pump |
Average energy consumption | 1500Watt average | 20kW pump |
24-40kW electricity | 22-35kW electricity | |
Laser gas (oxygen, helium, nitrogen) | WaterAbrasive grit | |
Disposal of cutting wastes such as water & grit | ||
Minimum size of cutting slit | 0.15mm | 0.5mm |
Cut surface appearance | striated | “sand-blasted” appearance |
Processing tolerance | 0.05mm | 0.2mm |
Degree of burring | None | Partial |
Thermal stress on material | Deformation, tempering, structural changes may occur | No thermal stress |
Personal safety requirements | None | Safety glasses, ear protection, protection from high pressure water |
Production of gases | some | None |
Noise pollution | Very low | Very high |
Machine clean up requirements | Low | Very high |
Cutting waste produced | Dust requiring vacuum extraction and filtering | Large quantities of water and grit |
Verdict: Laser cutting is faster, more precise and generates fewer running costs and waste materials than the waterjet, but is limited by material types and thicknesses.
Plasma Cutting
Used only on metals, plasma cutting can cut through thick sheets that a laser can’t. The plasma arc cutting process uses electrically conductive gas to transfer energy through the plasma cutting torch to the metal being cut. Like laser cutting, a plasma cutter cannot cut through plastics or woods, but like the waterjet it can cut through thick metals. Also like the laser, plasma melts the metal to pierce through it and has a high level of accuracy.
The table below shows the comparison between our current laser cutter and plasma cutting:
Our Amada F1 CO2 Laser | Plasma Cutting | |
Energy used | Light | |
Source of energy | Gas powered laser beam | DC power supply |
Transmission of energy | Laser beam guided by mirrors | Electrically charged gas |
Maximum permissible tolerance & distance between material and nozzle | +/- 0.1mm | +/- 0.5mm |
Physical Machine Set Up | Laser source located inside the machine | Working area, shop air and plasma torch |
Beam output | 1500 to 4000W | N/A |
3D Material Cutting (tubes) | Not possible due to rigid beam and strict CAD regulation of distance to nozzle | N/A |
Materials able to be cut | Metals, excluding reflective metals such as brass | All metals |
Material thicknesses able to cut | Up to 25mm Mild Steels, 12mm Stainless Steels, 10mm Aluminium | Maximum 10mm |
Common applications | Cutting flat sheet metals | Cutting flat sheet and plate |
Parts that will wear out with use | Protective glass, gas nozzle, mirrors | Cutting nozzles & electrodes |
Average energy consumption | 1500Watt average | 300amp plasma |
24-40kW electricity | 55kW electricity | |
Laser gas (oxygen, helium, nitrogen) | ||
Minimum size of cutting slit | 0.15mm | 0.05mm |
Cut surface appearance | striated | Striated |
Processing tolerance | 0.05mm | 0.5mm |
Degree of burring | None | Partial |
Thermal stress on material | Deformation, tempering, structural changes may occur | Deformation, tempering, structural changes may occur |
Personal safety requirements | none | Protective safety glasses |
Production of gases | some | Some |
Noise pollution | Very low | Medium |
Machine clean up requirements | Low | Medium |
Cutting waste produced | Dust requiring vacuum extraction and filtering | Dust requiring vacuum extraction and filtering |
Verdict: while laser cutting and plasma cutting share a great many similarities in process and precision, tolerances, energy consumption and required protection of laser cutting is considerably lower, making this method superior in the industrial field of sheet metal cutting.
Flame Cutting aka Oxyfuel Gas Cutting
This method involves several cutting processes used to cut metals through the chemical reaction of oxygen with the base metal at high temperatures maintained by a flame. A jet of pure oxygen is streamed into the heated area causing a chemical reaction that forms iron oxide (also known as “slag”). The oxygen steam blows away the slag allowing the metal below to be pierced and cut. This cutting method is limited to carbon and low alloy variants of steel.
Our Amada F1 CO2 Laser | Oxyfuel Gas Cutting | |
Energy used | Light | Oxygen & acetylene |
Source of energy | Gas powered laser beam | Oxy-acetylene |
Transmission of energy | Laser beam guided by mirrors | Gas flame through a torch |
Maximum permissible tolerance & distance between material and nozzle | +/- 0.1mm | 0.5mm |
Physical Machine Set Up | Laser source located inside the machine | Gases, cutting torch & work area |
Beam output | 1500 to 4000W | N/A |
3D Material Cutting (tubes) | Not possible due to rigid beam and strict CAD regulation of distance to nozzle | N/A |
Materials able to be cut | Metals, excluding reflective metals such as brass | Carbon steels, most metal alloys |
Material thicknesses able to cut | Up to 25mm Mild Steels, 12mm Stainless Steels, 10mm Aluminium | 3mm to 10mm |
Common applications | Cutting flat sheet metals | Cutting flat sheet metals |
Parts that will wear out with use | Protective glass, gas nozzle, mirrors | Cutting torch tips |
Average energy consumption | 1500Watt average | HR plate |
24-40kW electricity | No electricity | |
Laser gas (oxygen, helium, nitrogen) | Oxygen gas | |
Acetylene | ||
Minimum size of cutting slit | 0.15mm | 0.5mm |
Cut surface appearance | striated | Striated |
Processing tolerance | 0.05mm | 0.76mm |
Degree of burring | None | Partial |
Thermal stress on material | Deformation, tempering, structural changes may occur | Deformation, tempering, structural changes may occur |
Personal safety requirements | none | Protective safety glasses and gloves |
Production of gases | some | Some |
Noise pollution | Very low | Low |
Machine clean up requirements | Low | Medium |
Cutting waste produced | Dust requiring vacuum extraction and filtering | Mainly dust |
Verdict: Laser cutting is more precise, faster and able to cut a wider range of metals than flame cutting. Although flame cutting requires no electricity, making it more cost effective than laser on the surface, by being faster and more efficient laser cutting is the superior choice. Also, laser is much safer as flame cutting is completed by hand using a torch.
Mechanical Cutting
Mechanical cutting can be used as a supplement to laser cutting, or as a distinct service of its own. Preference between the two methods is usually concerned with application requirements, cost-effectiveness, production capabilities and customer needs. Mechanical cutting includes tooling and machining and is a process utilising power driven equipment to cut material; equipment such as a lathe, milling machine, drills and mechanical saws. At Yorkshire Profiles we cut all sheet metal with our F1 laser, but we have the capability through our circular saw and band saw, to cut through tube lengths and smaller sections of metal for welding (yes, we weld too!).
A milling machine, perhaps the most applicable of the mechanical cutting machines as it is large and doesn’t require a person to operate it directly (as with a band saw or circular saw), is a stationary cutting tool and moveable table on which the material is positioned and clamped. In this machine it is the table that moves rather than the cutting tool, with computer directions determining the movement of the table around the rotating blade.
Our Amada F1 CO2 Laser | Mill Cutting | |
Energy used | Light | Metal blade |
Source of energy | Gas powered laser beam | Electrical supply |
Transmission of energy | Laser beam guided by mirrors | Electrical supply turns blade |
Maximum permissible tolerance & distance between material and nozzle | +/- 0.1mm | Blade itself goes through material. Tolerance variable depending on blade size |
Physical Machine Set Up | Laser source located inside the machine | Moveable table & fixed, rotating blade |
Beam output | 1500 to 4000W | N/A |
3D Material Cutting (tubes) | Not possible due to rigid beam and strict CAD regulation of distance to nozzle | Partially possible, if it can be fixed to the table |
Materials able to be cut | Metals, excluding reflective metals such as brass | All materials |
Material thicknesses able to cut | Up to 25mm Mild Steels, 12mm Stainless Steels, 10mm Aluminium | Up to 20cm in most materials |
Common applications | Cutting flat sheet metals | Cutting wood and metal sheets |
Parts that will wear out with use | Protective glass, gas nozzle, mirrors | Table moveable parts, blades (frequently) |
Average energy consumption | 1500Watt average | |
24-40kW electricity | ||
Laser gas (oxygen, helium, nitrogen) | ||
Minimum size of cutting slit | 0.15mm | 2mm |
Cut surface appearance | striated | Straight |
Processing tolerance | 0.05mm | 1mm |
Degree of burring | None | Some |
Thermal stress on material | Deformation, tempering, structural changes may occur | Some |
Personal safety requirements | none | Gloves, eye protection |
Production of gases | some | None |
Noise pollution | Very low | Medium |
Machine clean up requirements | Low | Medium |
Cutting waste produced | Dust requiring vacuum extraction and filtering | Mostly dust |
Verdict: Laser is a vastly superior method of cutting both in terms of precision and tolerances, but compared with mechanical cutting processes is considerably more expensive to operate. However, as with our previous set up with both a waterjet and a laser, and our current set up of a laser and fabrication cutting tools such as our band saw, these two cutting processes are not mutually exclusive.
Conclusion: Laser or the Alternatives?
With all of these cutting methods available, it boils down to what is being cut as to which method is best for a consumer, and to what to cut, how and for how much when it comes to purchasing machinery as an operator. As we have shown through our evolution as a company, once you choose one method as a profiling company, you are not stuck for life in one realm of cutting. We went from a waterjet, to a combination, to only the laser and now include fabrication cutting processes through our saws (not forgetting that we can also bend and weld now too!)
The reliability of laser in its precision cutting and CAD programming is our primary reasoning for providing this service as the main part of our profiling portfolio. We chose laser over all other cutting methods because for us and for our customers, it is the best choice. And with fibre lasers now available it is an ever growing and evolving method of cutting. We can’t wait to have a more powerful and faster laser installed here at YPL!
The choice is yours when it comes to your own cutting needs. The questions to ask are:
- what are you cutting – material, thickness, and size?
- How much do you have to spend in terms of time and money?
- How much precision do you need in your cut and what are your tolerances?
Alternatively, give us a call at Yorkshire Profiles (01904 737095) or email sales@yorkshireprofiles.co.uk and we’ll be happy to work through these questions with you and discover together if our F1 laser is the way forward for your cutting needs!